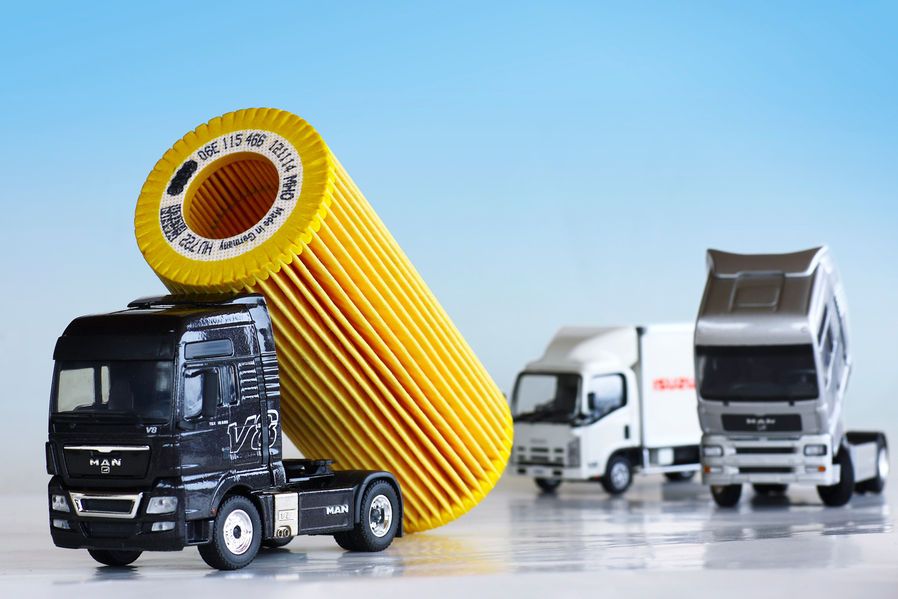
Im Motor entstehen bei der Verbrennung zahlreiche Schadstoffe wie Rußpartikel, Staub und Metallabrieb. Diese können Störungen verursachen. Die Aufgabe der Filter ist es daher, die Schadstoffe aufzunehmen und so unschädlich zu machen. Gerade in Nutzfahrzeugen sind diese starken Belastungen ausgesetzt. Sie müssen Drücke von mehr als 20 bar aushalten, Temperaturen bis 140 Grad widerstehen und jede Menge Partikel schlucken. In den Anfängen der motorisierten Lastenverkehre reichte noch ein Stück Filz aus, um das gröbste aus Motoröl, Diesel oder Luft zu holen. Heutzutage sind solche Filter hoch technisierte und aufwendig herzustellende Produkte.
Vom einfachen Filz zum Hightech-Vlies
Aus dem Filz von damals hat sich dank veränderter Verbrennungs- und Einspritzverfahren, neuer Kraft- und Schmierstoffe, variabler Ventiltriebe, innovativer Aufladungstechniken und nicht zuletzt immer strengerer Abgasgrenzwerte ein Hightech-Produkt entwickelt. Wie sich die Filtertechnik im Lauf der Zeit verändert hat, zeigt unter anderem die Motorölfilterung. Allein die Wechselintervalle des Motoröls haben sich angesichts von Ölzustandssensoren und optimierten, vollsynthetischen Schmierstoffen in den vergangenen 20 Jahren verdreifacht.
Bei den ersten Motoren waren noch Nebenstromfilter im Einsatz. Rund zehn Prozent des Ölstroms zweigten die Konstrukteure ab, filtrierten ihn und führten anschließend das Öl dem Hauptstrom wieder zu. Schwachpunkt dieser Vorgehensweise: Der Nebenstrom war zwar von Partikeln gereinigt, der größere restliche Teil des Öls enthielt aber weiter Teilchen, die die empfindlichen Zylinderlaufflächen beschädigen konnten. Das änderte sich erst mit der Hauptstromfilterung.
Dabei zeigt sich in der Praxis aber eine andere Schwierigkeit: Setzt sich der Filter im Laufe der Zeit zu, lässt er immer weniger Öl durch, gleichzeitig steigt der Druck an der Außenseite an und das Medium droht zu kollabieren. Die Lösung des Dilemmas brachte ein Überdruckventil, inzwischen eines der wichtigsten Bauteile im Gehäuse.
Ein Bypass-Ventil beugt Verstopfung vor
Drohen die Schadstoffe den Ölfilter zu verstopfen, öffnet das Druckventil einen Bypass und verhindert damit, dass der Motor zu wenig oder überhaupt kein Öl mehr bekommt. Dabei strömt das Öl am Filtermedium vorbei zum Motor. Das hat wiederum ebenfalls Nachteile. Die Ölversorgung funktioniert zwar wieder. Allerdings gelangt dann ungefiltertes Öl an die Schmierstellen. Es besteht also die Gefahr, dass abrasive Teilchen den Motor schädigen.
Auch ein Kaltstart bei extrem tiefen Temperaturen kann dazu führen, dass sich das Überdruckventil öffnet. Dann ist das Motoröl sehr zähflüssig. Daher lässt es sich nur unter erhöhtem Druck durch den Filter pressen. Bevor der Druck, der dabei entsteht zu hoch wird, öffnet daher das Ventil. Damit das Druckventil unter normalen Einsatzbedingungen von Ölwechsel zu Ölwechsel geschlossen bleibt, muss der Filter eine möglichst große Schmutzaufnahmekapazität besitzen. Hier unterscheiden sich Qualitätsfilter von Billigprodukten.
Filterhersteller wie Mann und Hummel, Mahle oder Hengst bauen schon längst nicht mehr bloße Filtereinsätze. Seit Jahren geht der Trend zur modularen Bauweise, die eine Reihe von Funktionen einschließt. Mit der Abgasnorm Euro 6 gehören dazu unter anderem die Kühlung des Motoröls, der Luftmassenmesser oder die Blow-by-Gas-Filterung.
Längere Wechselintervalle mit neuen Materialien
Immer längere Wartungsintervalle stellen die Filterproduzenten vor große Herausforderungen. Über ausreichend hohe Standzeiten entscheidet vor allem die Wahl des Filtermediums. Papier, bzw. Cellulose-Filter setzen sich immer mehr gegen den Filz-Filter durch. Je nach Fahrzeug und Einsatzzweck werden aber inzwischen auch Mischfasern oder mehrlagige Filter verwendet, beispielsweise eine mit einem Spinnvlies gekapselte Glasfaserlage. Die meisten Kraftstoff- und Luftfilter sind mit Cellulose oder Mischungen aus synthetischen Fasern sowie Glasfasern bestückt. Die Entwicklung tendiert zu immer feineren Filtermedien und vollsynthetischen Filterelementen.
Was muss ein Motorölfilter können? „Unser Filterelement aus einer Mischfaser aus Cellulose und Polyester für die aktuellen MAN-Motoren bietet einen Abscheidegrad von deutlich über 99 Prozent bei einer Partikelgröße von 38 Mikrometern“, sagt Matthias Weller, Mann-Filter-Produktmanager für Lkw und Busse beim Filterhersteller Mann und Hummel. Eine wichtige Rolle spielt die Faseranordnung des Filtermediums. An der Außenseite liegen die Fasern nur lose beieinander, in Richtung Innenseite sind sie zunehmend dichter miteinander verflochten. Durch diese Struktur dringt Feinschmutz weit in das Filtermedium ein, während gröbere Partikel an der Außenseite abgehalten werden.
Schadstoffe lagern sich als Filterkuchen ab
Auf dem Filter sammeln sich Partikel und bilden Schicht für Schicht den sogenannten Filterkuchen. Im Laufe der Filtration nimmt seine Schichtdicke zu. Die Leistungsfähigkeit des Filters kann sich zwar dadurch erhöhen, dass die auf der Oberfläche bereits vorhandenen Partikel weitere Schmutzteilchen daran hindern, in den Filter vorzudringen. Viele Filter erreichen daher erst nach kurzer Anlaufzeit ihre angegebene Leistung. Setzt sich der Filter mit der Zeit aber zu stark zu, steigt auch der Strömungswiderstand entsprechend. Dabei nimmt der Volumenstrom durch den Filter entweder ab oder der steigende Druck bewirkt eine Kuchenkompression. Der Filterkuchen verdichtet dann schlagartig und verstopft den Filter komplett.
Je feiner das Filtermedium, desto schneller setzt es sich naturgemäß zu. Damit dennoch vernünftige Standzeiten zu realisieren sind, versuchen die Hersteller, die Oberfläche des Filtermediums so groß wie möglich zu gestalten. „Das Luftfilterelement von Mann Filter für den Mercedes Actros der dritten Generation deckt eine Fläche von rund 12,5 Quadratmetern ab“, sagt Matthias Weller. Abgewickelt kommt das Papier auf eine Seitenlänge von mehr als 30 Metern.
Größere Oberflächen bei immer weniger Bauraum
Gleichzeitig gestehen Motorenentwickler den Filterkomponenten immer weniger Bauraum zu. Es geht also nicht ohne kompakte Abmessungen. Um eine möglichst große Fläche Platz sparend in ein Gehäuse zu bekommen, sind Falttechniken im Einsatz, die manchen Origamikünstler zum Staunen bringen dürften. Damit die Falten nicht zusammenkleben und den Filter so selbst zusetzen, sind kleine Stege in das Material geprägt. Vor allem beim Kaltstart des Motors können sich ätzende Säuren bilden. Um den Filter davor zu schützen sind die Fasern mit Phenolharz imprägniert, was dem Filtermedium gleichzeitig mehr Stabilität gibt. Damit das Filtermaterial durch den beim Motorbetrieb entstehenden Druck nicht in sich zusammenfällt, stützt es zusätzlich ein Kunststoffrohr im Innern des Gehäuses.
Weiter erhöht eine dichte Verbindung der Filterfalten zu den Endscheiben des Filters die Stabilität. In der Vergangenheit dienten dazu Metalldeckel mit einer Dichtung, die mit dem Papier verklebt waren. Die Verklebung riss aber oft ein und das Öl strömte samt Partikeln am Filter vorbei zum Motor. Hier behelfen sich die Hersteller inzwischen mit einer eleganteren Lösung: Das Filtermedium ist direkt in Kunststoff-Endkappen oder auch in Folienendscheiben eingeschweißt. Das Filterpapier ist so fester verbunden und soll sich zudem umweltschonender entsorgen lassen, da es rückstandslos verbrennt.
Biodiesel ist Gift für Standardfilter
Eine jüngere Belastungsquelle sind alternativer Kraftstoffe die dem Diesel beigemischt werden. Zwangsläufig sammelt sich dadurch auch im Motoröl dieser Biodiesel an. Bei hohen Temperaturen entstehen aggressive Bedingungen, die dem Filter zusetzen. Es kommt zu starker Nitration des Öls. Diffundierender Stickstoff versprödet das Material, die Schmutzaufnahmekapazität sinkt und der Filter verliert seine Funktionsfähigkeit. Das Rezept gegen solche Stickstoffattacken: mehr¬lagige Filter und Kunststofffasern. Filterspezialist Mann und Hummel setzt bei seinen aktuellen Filterelementen auf ein Medium aus Cellulose- und Polyester-Mischfasern.
Wie empfindlich mittlerweile die Einspritzsysteme moderner Lkw-Motoren sind, zeigt auch die Fertigung der Kraftstofffilter. Der Produktionsrau ist ein nach EN ISO 14644 zertifizierter Reinraum. Wände, Decken und Böden sind Schmutz abweisend. Belüftet werden die Räume über eine definierte Luftwechselrate. Damit keine Partikel von außen eindringen, ist der Druck leicht höher als in den ihn umgebenden Werkshallen.
Nanofasern sind die neueste Filtermode
Hoher Feinstaub- und Rußgehalt in der Luft setzt den hochsensiblen Einspritzsystemen und Komponenten des Motors ebenfalls zu. Beim Betrieb von Fahrzeugen in schadstoffbelasteter Umgebung setzt Mann und Hummel in Luftfiltersystemen inzwischen auf Nanofasern. Die Filter bestehen aus einem Trägermedium, auf das feinste Polymerfasern in hauchdünnen Schichten aufgebracht sind. Die Fasern haben einen Durchmesser von weniger als einem Mikrometer und sind somit 80 bis 300 Mal kleiner als die Fasern des Trägermaterials.
Die Leistung des Filters erhöht sich erheblich, je mehr Oberfläche zur Verfügung steht. Labortests mit 0,7 Mikrometer großen Partikeln haben laut Mann und Hummel einen Abscheidegrad des Trägermaterials von 40 Prozent nachgewiesen. Mit der Nanofaserbeschichtung soll sich der Abscheidegrad auf 99,97 Prozent erhöhen.